Is appliance repair a dying business? The question hangs heavy in the air, especially considering the rise of disposable income, readily available replacements, and the increasing prevalence of DIY solutions. This isn’t simply a matter of broken toasters; it’s a reflection of broader shifts in consumer behavior, technological advancements, and economic realities. Understanding these forces is crucial to grasping the future of this often-overlooked trade.
From the evolution of simple mechanical repairs to the complexities of modern smart appliances, the appliance repair industry has undergone a dramatic transformation. Extended warranties, initially designed to ease consumer concerns, have ironically impacted repair demand. Simultaneously, the rise of DIY culture, fueled by readily accessible online tutorials and readily available parts, further challenges traditional repair services. The economic landscape also plays a significant role, with recessionary periods influencing repair versus replacement decisions based on disposable income levels.
The Shifting Landscape of Home Repair
The appliance repair industry, once a cornerstone of local economies, is navigating a complex and evolving landscape. Technological advancements, shifting consumer behaviors, and economic pressures are all contributing to a transformation that is reshaping the way we maintain our homes and appliances. This evolution necessitates a closer examination of the forces at play and their impact on the future of appliance repair businesses.
Evolution of Appliance Repair
Historically, appliance repair was a predominantly local service, with independent technicians providing essential repair services for a community. Repair was often the most economical option, and consumers valued the longevity and repairability of their appliances. However, the rise of mass-produced, less-repairable appliances, coupled with extended warranties and the ease of online purchasing, has altered this dynamic. The shift towards planned obsolescence, where appliances are designed with shorter lifespans, has also played a significant role. This has led to a decrease in the demand for repair services in some sectors, while simultaneously increasing the demand for specialized technicians capable of handling increasingly complex electronics.
Impact of Extended Warranties
Extended warranties have significantly impacted the appliance repair industry. While offering consumers peace of mind, they often channel repairs through specific service providers, reducing the number of jobs available to independent technicians. Manufacturers often negotiate favorable rates with these providers, potentially squeezing profit margins for independent businesses. The prevalence of extended warranties, therefore, represents both an opportunity and a challenge for the industry. While some repair businesses may partner with warranty providers, others face increased competition and reduced customer base.
The Rise of DIY Home Repair
The proliferation of online resources, including instructional videos and detailed repair guides, has empowered many homeowners to attempt DIY repairs. Websites and platforms dedicated to home improvement provide step-by-step instructions and readily available parts, making it easier than ever to fix minor appliance issues. This rise in DIY culture has undoubtedly reduced the demand for some types of repairs, particularly those involving simple troubleshooting and component replacement. However, it is important to note that complex repairs often still require the expertise of a professional.
Repair Versus Replacement Costs
The decision to repair or replace an appliance is often driven by cost considerations. The following table provides a comparison of typical repair and replacement costs for common household appliances. These figures are estimates and can vary significantly based on factors such as the appliance’s age, brand, and the specific repair needed.
Appliance | Average Repair Cost | Average Replacement Cost | Repair vs. Replacement |
---|---|---|---|
Refrigerator | $150 – $400 | $800 – $2000 | Repair often more economical unless major component failure |
Washing Machine | $100 – $300 | $600 – $1500 | Repair can be cost-effective for minor issues |
Dishwasher | $120 – $350 | $700 – $1800 | Repair is usually a more viable option than replacement |
Oven | $150 – $500 | $1000 – $3000 | Repair cost-effective unless multiple components are failing |
Economic Factors Affecting Demand: Is Appliance Repair A Dying Business
The appliance repair industry’s viability is intrinsically linked to broader economic trends. Fluctuations in consumer spending, disposable income, and energy prices significantly impact the demand for repair services versus outright appliance replacement. Understanding these economic factors is crucial for predicting the industry’s future trajectory.
Economic recessions exert a powerful influence on appliance repair demand. During periods of economic downturn, consumers often delay or forgo discretionary spending, including non-essential home repairs. This leads to a decrease in demand for appliance repair services as individuals prioritize essential expenses and postpone repairs until their financial situation improves. Conversely, during economic booms, increased disposable income might lead to a rise in repair requests, as people are more willing to invest in maintaining existing appliances rather than purchasing new ones.
Recessions and Appliance Repair Demand, Is appliance repair a dying business
During a recession, consumers are more likely to attempt DIY repairs or postpone repairs altogether, leading to a decline in demand for professional services. The 2008 financial crisis, for example, saw a noticeable dip in appliance repair business for many companies, as consumers tightened their belts and prioritized essential spending. This trend is often observed across various socioeconomic groups, though the impact might be more pronounced among lower-income households. Data from the U.S. Census Bureau on consumer spending during recessionary periods could provide further quantitative evidence supporting this observation.
Disposable Income and Appliance Repair Frequency
The relationship between disposable income and appliance repair frequency is generally positive. Higher disposable income correlates with a greater willingness to invest in appliance repair, rather than replacement. Individuals with higher incomes may opt for professional repair services more frequently, even for minor issues, minimizing downtime and ensuring optimal appliance performance. Conversely, lower-income households might delay repairs until the appliance malfunctions completely, necessitating a more expensive replacement. This difference in approach reflects a trade-off between immediate cost and long-term appliance lifespan.
Rising Energy Costs and Appliance Lifespan
Rising energy costs can indirectly influence appliance repair needs. As energy prices increase, consumers become more conscious of their energy consumption. This increased awareness might lead to more frequent maintenance and repairs to ensure appliances operate efficiently, thereby extending their lifespan and reducing long-term energy expenditure. For instance, a refrigerator with a faulty seal leading to increased energy consumption might prompt a repair to avoid higher electricity bills. Conversely, if the repair cost is excessively high compared to the cost of a new energy-efficient model, replacement becomes more economically viable.
Economic Class and Appliance Repair Decisions
Different economic classes approach appliance repair or replacement differently. Higher-income households tend to favor professional repair services and prioritize maintaining their appliances, often opting for repairs even for minor issues. They might also invest in higher-quality appliances with longer lifespans, reducing the frequency of repairs and replacements in the long run. Lower-income households, however, often face a trade-off between repair costs and replacement costs. They might attempt DIY repairs or delay repairs until the appliance fails completely, often leading to replacement with a less expensive, potentially lower-quality appliance. This disparity reflects the differing financial priorities and risk tolerance across socioeconomic groups.
Technological Advancements and Their Impact
Technological advancements are profoundly reshaping the appliance repair landscape, impacting both the frequency of repairs and the methods used to address them. The increasing sophistication of appliances, coupled with improvements in manufacturing and diagnostic tools, presents both opportunities and challenges for the industry.
Smart appliances, with their embedded sensors and internet connectivity, offer a double-edged sword. While their increased functionality can lead to more complex malfunctions requiring specialized expertise, the remote diagnostic capabilities they offer are revolutionizing repair processes. Improved manufacturing techniques, focusing on durability and longevity, also contribute to a decrease in the overall repair rate, potentially affecting the long-term viability of the business.
Smart Appliances and Connectivity Affect Repair Needs
The integration of smart technology into appliances has created a new category of repair challenges. While smart features enhance user experience, they also introduce more points of potential failure. For instance, a malfunctioning Wi-Fi module in a smart refrigerator might require specialized knowledge beyond the typical repair technician’s expertise. Conversely, remote diagnostics via app connectivity allows for quicker identification of issues, potentially reducing the need for on-site visits and associated costs. This shift necessitates a workforce capable of handling both traditional mechanical repairs and software-related issues. The increased complexity of smart appliances might lead to longer repair times and higher repair costs, impacting consumer choices and influencing the demand for repair services. A smart oven with a faulty control board, for example, might require replacement of the entire unit rather than a simple component fix.
Improved Appliance Manufacturing and Repair Rates
Modern manufacturing processes have led to significant improvements in appliance durability. The use of higher-quality materials, advanced manufacturing techniques, and rigorous quality control measures result in appliances that are less prone to breakdowns. This increased longevity directly translates to a lower demand for repair services. For example, manufacturers are incorporating robust components and better insulation in refrigerators, leading to fewer compressor failures. This trend, while positive for consumers, presents a challenge to the appliance repair industry, requiring adaptation to a potentially reduced repair volume. Businesses may need to diversify their services or focus on niche repair areas to maintain profitability.
Technology in Remote Appliance Diagnosis and Repair
Remote diagnostics are rapidly changing how appliance repairs are handled. Smart appliances often transmit diagnostic data to manufacturers or service providers, enabling technicians to identify problems remotely. This allows for faster troubleshooting, quicker ordering of necessary parts, and potentially reduced on-site visits. The use of augmented reality (AR) technology is further enhancing remote diagnostics, enabling technicians to provide visual guidance to customers during repairs, empowering some users to handle minor fixes independently. However, reliance on remote diagnostics might not always be feasible, particularly for older appliances lacking smart features or for complex issues requiring physical examination. The effective integration of remote technologies requires robust internet connectivity and user familiarity with technology.
Examples of Technological Advancements Simplifying or Complicating Appliance Repair
The advent of modular design in appliances simplifies repairs by allowing for the easy replacement of individual components. This reduces downtime and lowers repair costs, as only the faulty module needs replacing. However, the increased complexity of electronics within appliances, particularly in smart appliances, can complicate repairs. A simple power surge could damage a complex circuit board, requiring extensive diagnostics and potentially costly replacements. For example, the widespread adoption of inverter technology in washing machines, while offering energy efficiency, has also introduced new challenges for repair technicians requiring specialized knowledge of electronic control systems. The shift towards integrated systems, where multiple components are interconnected, can also complicate diagnostics and repair procedures, increasing the overall cost and complexity of repairs.
The Changing Skillset of Appliance Repair Technicians
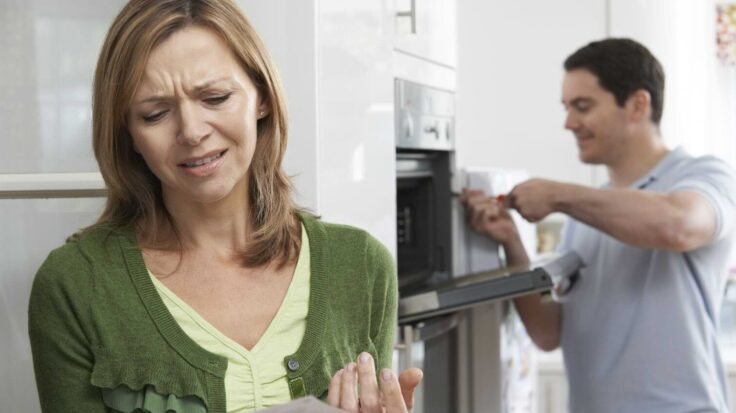
The appliance repair profession, while facing evolving challenges, is also undergoing a significant transformation in the required skillset of its technicians. The shift from primarily mechanical expertise to a blend of mechanical, electronic, and software proficiency is reshaping the industry and demanding a new level of specialized training. This evolution is driven by the increasing complexity of modern appliances, the integration of smart technology, and the growing emphasis on efficient and environmentally conscious repair practices.
The skills necessary for modern appliance repair extend far beyond the basic mechanical aptitude needed in the past. While a strong understanding of mechanical systems remains crucial for diagnosing and repairing fundamental components, today’s technicians must also possess advanced knowledge of electronics, embedded systems, and software programming. The prevalence of digital control boards, microprocessor-based components, and internet connectivity in contemporary appliances demands a multidisciplinary approach to troubleshooting and repair. Furthermore, a deep understanding of environmental regulations and sustainable repair practices is becoming increasingly important, as consumers and regulatory bodies are placing a greater emphasis on responsible disposal and repair methods.
Specialized Training and Certifications for Technicians
The need for a more diverse skillset necessitates specialized training and certification programs. These programs provide technicians with the in-depth knowledge and practical experience required to handle the complexities of modern appliances. Certifications from reputable organizations not only validate a technician’s expertise but also build consumer confidence. For instance, manufacturers often offer specialized training programs for their specific appliance lines, equipping technicians with detailed product knowledge and troubleshooting techniques. Industry associations also provide comprehensive certification programs that cover a wide range of appliance types and repair procedures, ensuring technicians possess the necessary skills across the board. These certifications demonstrate competency and often lead to higher earning potential for qualified technicians.
Challenges Faced by Experienced Technicians Adapting to New Technologies
Experienced technicians, while possessing valuable mechanical skills developed over years of experience, often face challenges adapting to the rapid advancements in appliance technology. The transition from primarily mechanical repairs to those involving complex electronics and software requires significant retraining and upskilling. This can be a steep learning curve, requiring considerable time and effort to master new diagnostic tools, software interfaces, and repair techniques. Furthermore, access to updated training resources and the financial burden of obtaining new certifications can pose significant obstacles for experienced technicians seeking to remain competitive in the evolving market. Many companies are now offering apprenticeships and on-the-job training programs to bridge this gap, recognizing the importance of integrating experienced technicians’ knowledge with modern technical skills.
The Potential for Automation in Appliance Repair and its Impact on Employment
The increasing sophistication of appliances and the development of advanced diagnostic tools are paving the way for automation in appliance repair. Automated diagnostic systems can quickly identify malfunctions, reducing the time and expertise needed for initial troubleshooting. While this may lead to some displacement of entry-level positions, the overall impact on employment is likely to be complex. The demand for highly skilled technicians capable of interpreting automated diagnostics, performing complex repairs, and integrating new technologies is expected to remain strong. Moreover, the increasing complexity of smart appliances will likely necessitate a greater need for specialized technicians proficient in software and network troubleshooting. For example, the integration of AI-powered diagnostics into repair tools might allow for faster diagnosis, but a skilled technician will still be needed to interpret the results and perform the necessary repairs. Therefore, the future of appliance repair is likely to involve a shift towards higher-skilled roles requiring advanced training and expertise, rather than a complete replacement of human technicians.
Consumer Behavior and Repair Choices
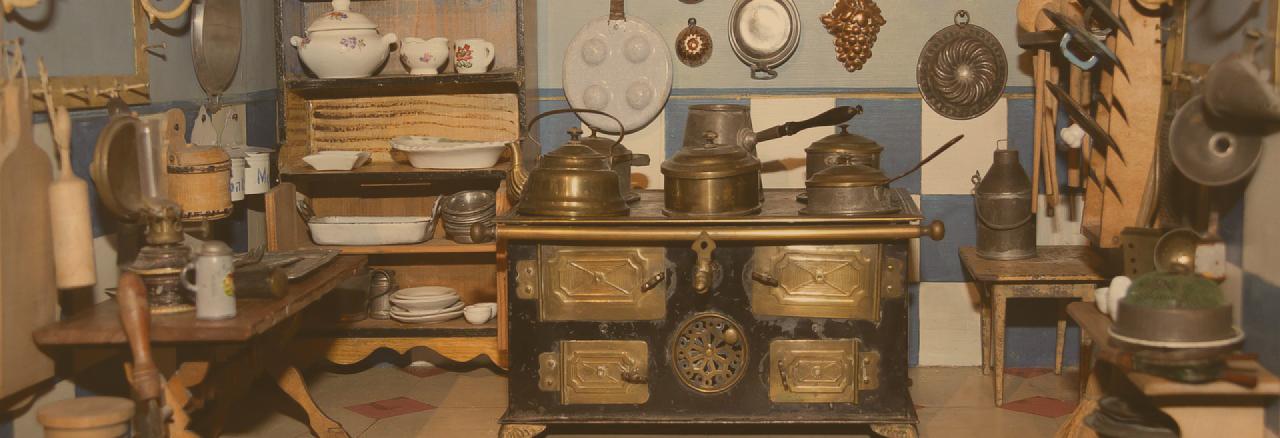
Consumers’ decisions regarding appliance repair versus replacement are complex, influenced by a multitude of intertwined factors. These factors range from the perceived cost-effectiveness of repair compared to the purchase price of a new appliance, to the emotional attachment to a particular item, and increasingly, to environmental considerations. Understanding these nuances is crucial for both appliance repair businesses and manufacturers seeking to navigate the evolving market.
The decision to repair or replace hinges primarily on a cost-benefit analysis. Consumers weigh the cost of repair, including parts, labor, and potential downtime, against the cost of purchasing a new appliance, factoring in features, energy efficiency, and warranty. The age and overall condition of the appliance also play a significant role. An older, less efficient appliance might be deemed more cost-effective to replace than to repair repeatedly. Conversely, a relatively new, high-value appliance with a significant repair cost might still be deemed worth repairing, especially if the repair extends its lifespan considerably. Brand loyalty and personal preferences also subtly influence these choices. A consumer with a positive experience with a particular brand might be more inclined to repair an existing appliance than to switch to a different brand.
Factors Influencing Repair or Replacement Decisions
Several key factors consistently shape consumer decisions. Cost is paramount, with consumers carefully comparing the total cost of repair (including parts, labor, and potential service calls) against the price of a new appliance. The appliance’s age and remaining useful life are equally important considerations. A relatively new, high-value appliance might warrant repair, while an older, less efficient model might be more economically replaced. The appliance’s functionality also plays a significant role; a critical failure might necessitate replacement, while a minor malfunction might be economically repaired. Finally, personal attachment and brand loyalty can subtly influence the decision, with some consumers preferring to repair their familiar appliances rather than purchase new ones.
The Role of Online Reviews and Ratings in Choosing a Repair Service
In today’s digital age, online reviews and ratings significantly impact consumer choices when selecting an appliance repair service. Platforms like Yelp, Google Reviews, and Angie’s List provide readily accessible feedback from previous customers, influencing trust and confidence in a particular service provider. Positive reviews highlighting professionalism, expertise, and fair pricing can significantly boost a repair business’s reputation and attract new customers. Conversely, negative reviews detailing poor service, excessive charges, or unresolved issues can deter potential customers and damage a business’s reputation. Consumers often prioritize services with high average ratings and a large volume of reviews, suggesting a greater level of reliability and customer satisfaction.
The Impact of Environmental Concerns on Consumer Repair Choices
Growing environmental awareness is increasingly influencing consumer behavior regarding appliance repair. The environmental cost of manufacturing and disposing of appliances is becoming a significant consideration. Repairing an existing appliance extends its lifespan, reducing the demand for new production and associated environmental impacts like resource depletion and carbon emissions. Consumers are becoming more conscious of the “circular economy” concept, favoring repair and reuse over the immediate replacement of appliances. This shift is driven by both personal values and increasing awareness of the environmental consequences of consumerism. This growing trend is expected to further impact the appliance repair industry, driving demand for sustainable and environmentally friendly repair practices.
Pros and Cons of Repairing Versus Replacing Appliances
The decision to repair or replace an appliance involves weighing various advantages and disadvantages.
Before listing the pros and cons, it’s important to note that the optimal choice depends heavily on the specific appliance, its age, the nature of the malfunction, and the overall cost comparison.
- Repairing Appliances: Pros
- Lower upfront cost compared to replacement.
- Extends the lifespan of the appliance, reducing waste.
- Environmentally friendly option.
- Maintains familiarity with a trusted appliance.
- Repairing Appliances: Cons
- May involve recurring repair costs.
- Potential for temporary appliance downtime.
- Repair may not completely resolve the issue.
- May not be cost-effective for older or heavily damaged appliances.
- Replacing Appliances: Pros
- Eliminates recurring repair costs.
- Access to newer features and technologies.
- Improved energy efficiency.
- Warranty coverage for a set period.
- Replacing Appliances: Cons
- Higher upfront cost.
- Environmental impact of manufacturing and disposal.
- Potential for buyer’s remorse if a suitable replacement isn’t found.
- Loss of familiarity with a previously reliable appliance.
The Future of Appliance Repair

The appliance repair industry stands at a crossroads, facing both challenges and opportunities in the coming decade. Technological advancements, shifting consumer preferences, and economic fluctuations will all play significant roles in shaping its future. Understanding these forces is crucial for businesses and technicians alike to adapt and thrive.
The next five to ten years will likely witness a significant reshaping of the appliance repair landscape. While the core need for repair services will remain, the way those services are delivered and the types of repairs needed will evolve considerably.
Appliance Repair in Five and Ten Years
In five years, we can expect to see a rise in specialized repair services catering to high-end appliances and smart home technology. The increasing complexity of smart appliances will demand technicians with advanced skills in electronics and software troubleshooting. Simultaneously, the increased availability of readily accessible DIY repair resources and parts will likely lead to a decline in simple repairs, shifting the demand towards more complex issues. Ten years out, the landscape will be even more dramatically altered. Predictive maintenance enabled by IoT (Internet of Things) technology could become prevalent, reducing the frequency of major repairs. This shift would necessitate a transition for repair businesses towards proactive maintenance services and data-driven diagnostics. Furthermore, the rise of sustainable repair practices, focusing on component replacement rather than whole-unit replacements, could become a significant market driver. We might see more businesses specializing in eco-friendly repair methods and utilizing recycled parts. A hypothetical example: A large appliance repair chain, currently focused on in-home service calls, might expand into predictive maintenance contracts for high-end clients, utilizing remote diagnostics and scheduling preventative maintenance based on data analysis.
Potential New Business Models
Several new business models are poised to emerge within the appliance repair sector. Subscription-based maintenance plans, offering preventative care and priority service, could become increasingly popular, providing a stable revenue stream for repair businesses. Online platforms connecting customers with certified technicians, similar to ride-sharing services, could disrupt the traditional model of localized repair shops. Furthermore, specialized repair franchises focusing on specific appliance brands or types (e.g., a franchise solely focused on repairing high-end refrigerators) could gain traction. Another example is the development of mobile repair units equipped with advanced diagnostic tools and a wide inventory of common parts, allowing for faster and more efficient on-site repairs, minimizing customer downtime.
Changes in Consumer Behavior
Consumer behavior will significantly influence the future of appliance repair. The increasing preference for convenience will drive demand for faster, more efficient repair services, including same-day or next-day appointments and online booking systems. Consumers will also be more informed, leveraging online resources and reviews to choose reputable and reliable repair technicians. A growing environmental consciousness will encourage consumers to opt for repairs over replacements, extending the lifespan of their appliances and reducing electronic waste. Furthermore, the increasing affordability and availability of DIY repair kits and online tutorials will empower some consumers to tackle simpler repairs themselves, reducing the demand for basic service calls. This shift could be compared to the rise of home car maintenance – while professional mechanics still exist, many individuals now perform basic maintenance themselves, shifting the demand towards more complex repairs.