What does TAT mean in business? Understanding TAT, or turnaround time, is crucial for success in any industry. From project management to customer service and manufacturing, TAT significantly impacts efficiency, profitability, and customer satisfaction. This comprehensive guide explores the multifaceted role of TAT across various business sectors, offering practical strategies for optimization and highlighting the legal implications of missed deadlines.
We’ll delve into how TAT influences project timelines, resource allocation, and ultimately, the bottom line. We’ll examine best practices for communicating TAT expectations and explore the connection between TAT and customer loyalty. Furthermore, we’ll analyze the impact of TAT on supply chain management, manufacturing processes, and even legal contracts. By the end, you’ll have a clear understanding of how to leverage TAT to improve your business operations.
TAT in Project Management
Turnaround Time (TAT) is a critical factor in project management, directly impacting project timelines, resource allocation, and ultimately, project success. Understanding and effectively managing TAT ensures projects are completed efficiently and within budget. A well-defined TAT fosters clear communication and realistic expectations among team members and clients.
TAT’s Role in Setting Realistic Project Timelines
Establishing realistic project timelines hinges on accurate TAT estimations for each task. By breaking down a project into smaller, manageable tasks and assigning realistic TATs to each, project managers can create a comprehensive and achievable schedule. This involves considering factors such as task complexity, resource availability, and potential dependencies between tasks. Inaccurate TAT estimations can lead to unrealistic deadlines, causing project delays and impacting overall project success. For instance, if a web developer estimates a two-day TAT for designing a webpage but the actual TAT is five days, the entire project timeline will be affected.
TAT’s Impact on Resource Allocation
TAT directly influences resource allocation decisions. Projects with shorter TATs often require more resources to ensure timely completion. This might involve assigning more team members to a task, utilizing specialized tools or software, or outsourcing specific tasks. Conversely, projects with longer TATs may allow for more efficient resource allocation, potentially reducing overall project costs. For example, a project with a longer TAT might allow a single graphic designer to complete all the necessary design work, while a project with a short TAT might necessitate hiring additional designers to meet the deadline.
Communicating TAT Expectations
Clear and consistent communication of TAT expectations is crucial for both clients and team members. For clients, providing a detailed project timeline with clearly defined TATs for key milestones manages expectations and prevents misunderstandings. For team members, clear TAT expectations ensure everyone understands their responsibilities and deadlines, promoting accountability and efficient workflow. This can be achieved through regular project status meetings, progress reports, and the use of project management software that tracks task progress against allocated TATs.
Impact of Varying TATs on Project Costs
The following table illustrates how varying TATs can impact project costs. Shorter TATs generally lead to higher costs due to increased resource utilization, while longer TATs can lead to lower costs but may also increase the risk of project delays. It’s important to note that these are illustrative examples and actual costs will vary depending on several factors.
Project | TAT (Days) | Cost ($) | Impact |
---|---|---|---|
Website Development | 14 | 5000 | Moderate cost, manageable timeline |
Website Development | 7 | 7500 | Higher cost due to expedited timeline, requiring additional resources |
Logo Design | 3 | 500 | Low cost, short turnaround |
Logo Design | 10 | 300 | Lower cost, but potentially slower feedback and iteration cycles |
TAT in Customer Service
Turnaround Time (TAT) is a critical metric in customer service, representing the time it takes to resolve a customer’s issue or respond to their inquiry. A shorter TAT generally translates to higher customer satisfaction, while longer TATs can lead to frustration and churn. Effective management of TAT is essential for building a positive brand reputation and fostering customer loyalty.
The Relationship Between TAT and Customer Satisfaction
Customer satisfaction is directly correlated with the speed and efficiency of service delivery. A quick resolution to a problem demonstrates responsiveness and competence, leading to positive customer experiences. Conversely, lengthy TATs create negative experiences, increasing the likelihood of customer dissatisfaction and complaints. Studies consistently show a strong inverse relationship: as TAT increases, customer satisfaction decreases. For example, a company resolving customer issues within 24 hours might achieve a significantly higher satisfaction rating compared to a company taking several days. This difference can be substantial enough to impact customer retention and brand perception.
Strategies for Improving TAT in Customer Service Operations
Improving TAT requires a multifaceted approach focusing on process optimization and resource allocation. This includes streamlining workflows, implementing efficient ticketing systems, providing adequate training to customer service representatives, and leveraging technology such as AI-powered chatbots for initial response and issue triage. Investing in self-service options, like comprehensive FAQs and knowledge bases, can also reduce the volume of requests requiring direct agent intervention. Regularly analyzing performance metrics and identifying bottlenecks in the process allows for targeted improvements and proactive problem-solving. For instance, identifying a high volume of unresolved technical issues might indicate a need for additional training or improved documentation for agents.
Impact of Different TATs on Customer Loyalty
The impact of TAT on customer loyalty is significant. Customers who experience short TATs are more likely to remain loyal, recommend the company to others, and exhibit greater brand advocacy. Conversely, consistently long TATs lead to customer frustration, decreased trust, and an increased likelihood of switching to competitors. A study by [insert reputable source and findings here, e.g., a relevant research paper or industry report] showed a strong correlation between short TATs and increased customer lifetime value. This highlights the importance of prioritizing swift issue resolution as a key driver of customer retention and long-term profitability.
Setting and Monitoring TATs for Customer Service Requests
Effective TAT management requires a structured approach. The following steps Artikel a process for setting and monitoring TATs for customer service requests:
- Define Service Level Agreements (SLAs): Establish clear expectations for response and resolution times for different types of requests (e.g., high-priority, low-priority).
- Implement a Ticketing System: Use a system that tracks requests, monitors progress, and generates reports on TAT.
- Assign Ownership and Accountability: Clearly define roles and responsibilities for handling requests and meeting SLAs.
- Regularly Monitor Performance: Track TAT metrics against established SLAs and identify areas for improvement.
- Provide Regular Feedback: Share performance data with customer service representatives and provide coaching and support.
- Continuously Improve Processes: Regularly review and optimize workflows to reduce bottlenecks and improve efficiency.
TAT in Manufacturing and Production: What Does Tat Mean In Business
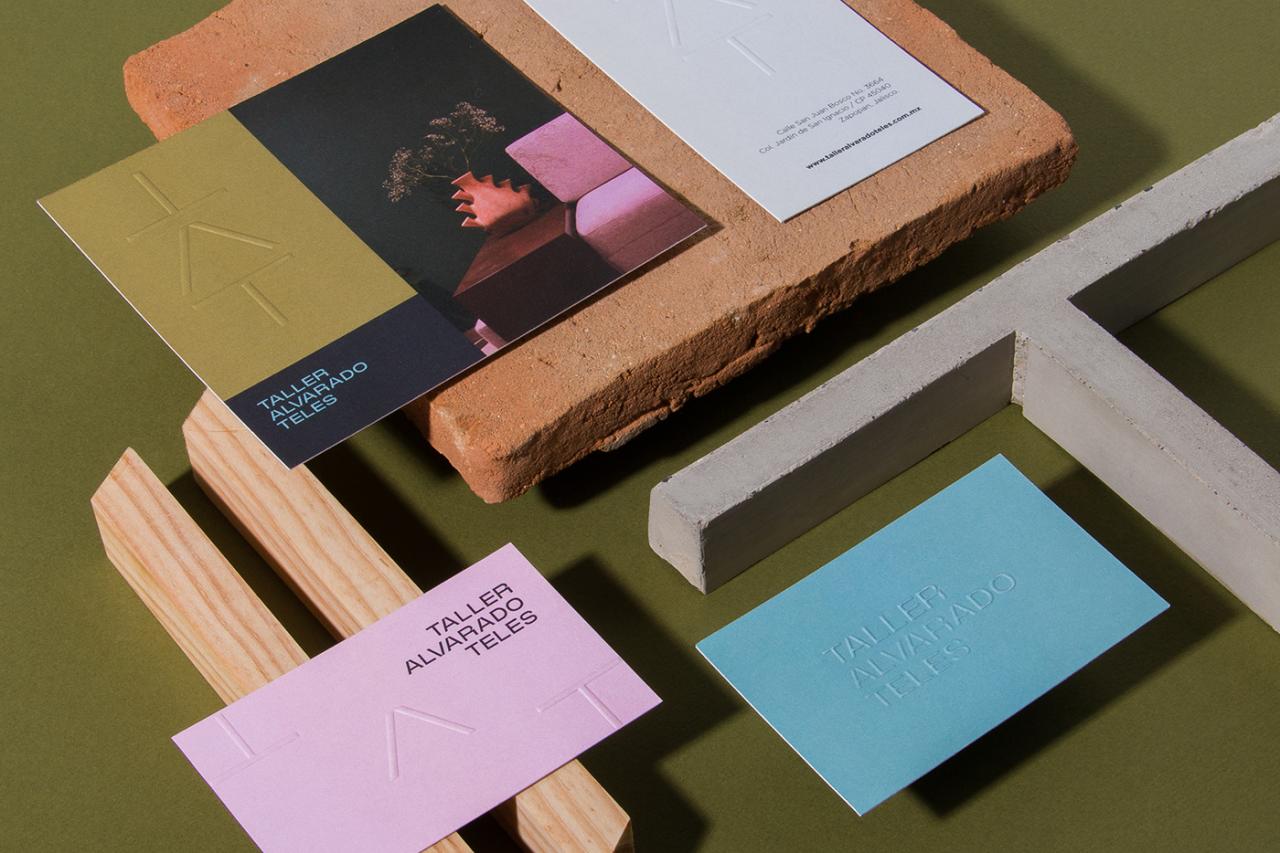
Turnaround Time (TAT) in manufacturing and production signifies the total time taken to complete a process, from receiving raw materials to delivering the finished product. Minimizing TAT is crucial for enhancing competitiveness, improving customer satisfaction, and maximizing profitability. Factors impacting TAT are numerous and interconnected, requiring a holistic approach to optimization.
Key Factors Influencing TAT in Manufacturing Processes
Several interconnected factors significantly influence the manufacturing process’s TAT. These factors span across various stages of production, from initial design and planning to final delivery. Understanding these factors is critical for effective TAT optimization strategies.
- Production Capacity and Equipment Utilization: Insufficient production capacity or inefficient equipment utilization directly increases TAT. Bottlenecks in the production line, caused by outdated machinery or insufficient workforce, lead to delays.
- Supply Chain Management: Delays in receiving raw materials or components due to inefficient supply chain management significantly impact TAT. Reliable suppliers with efficient delivery systems are crucial for maintaining optimal TAT.
- Process Efficiency and Automation: Streamlined processes and automation technologies are vital for reducing TAT. Manual processes are often slower and more prone to errors, whereas automation can significantly accelerate production and minimize human error.
- Inventory Management: Inefficient inventory management, including excessive stock or stockouts, can disrupt the production flow and extend TAT. Effective inventory management techniques like Just-in-Time (JIT) can significantly minimize delays.
- Quality Control Procedures: Rigorous quality control procedures are essential but can sometimes extend TAT if not properly integrated into the workflow. Efficient quality control methods that minimize disruptions are crucial for balancing quality and speed.
- Workforce Skills and Training: A well-trained and skilled workforce is crucial for efficient production. Inadequate training or lack of expertise can lead to errors and delays, thereby increasing TAT.
Methods for Optimizing TAT in Production
Optimizing TAT requires a strategic approach involving various methods. Different approaches may be suitable depending on the specific industry, production scale, and existing infrastructure.
- Lean Manufacturing Principles: Implementing Lean manufacturing principles, such as eliminating waste, optimizing workflow, and improving quality, can significantly reduce TAT. Examples include reducing lead times through JIT inventory management and streamlining production processes to minimize bottlenecks.
- Six Sigma Methodology: Utilizing Six Sigma methodologies focuses on reducing process variations and defects, thereby improving efficiency and reducing TAT. Statistical process control techniques are used to identify and eliminate the root causes of delays.
- Automation and Robotics: Integrating automation and robotics into the manufacturing process can significantly reduce TAT by automating repetitive tasks, improving accuracy, and increasing production speed. This is particularly effective in high-volume production environments.
- Improved Supply Chain Management: Implementing advanced supply chain management techniques, such as collaborative planning, forecasting, and replenishment (CPFR), can improve the predictability and efficiency of the supply chain, minimizing delays and improving TAT.
- Data Analytics and Predictive Modeling: Using data analytics and predictive modeling to identify potential bottlenecks and predict potential delays can enable proactive interventions and minimize disruptions to the production process.
Illustrative Flow Chart of a Manufacturing Process and Associated TATs, What does tat mean in business
The following flow chart illustrates a simplified manufacturing process, showing potential TATs for each stage. These TATs are illustrative and would vary significantly depending on the specific product, process, and manufacturing environment.
A simplified flow chart would depict stages like: Raw Material Procurement (TAT: 2-5 days), Production Planning (TAT: 1 day), Manufacturing (TAT: 7-14 days), Quality Control (TAT: 2 days), Packaging and Shipping (TAT: 1-3 days). The total TAT would be the sum of these individual TATs.
TAT in Supply Chain Management
Turnaround Time (TAT) is a critical metric in supply chain management, representing the total time taken to complete a process, from order placement to delivery. Efficient TAT directly impacts customer satisfaction, inventory levels, and overall supply chain profitability. Understanding and optimizing TAT across various stages is crucial for competitive advantage.
TAT’s Influence on Inventory and Warehousing
Effective TAT management significantly influences inventory management and warehousing strategies. Shorter TATs allow businesses to reduce safety stock, as the lead times for replenishment are minimized. This reduces storage costs, minimizes the risk of obsolescence, and frees up warehouse space for other purposes. Conversely, longer TATs necessitate higher safety stock levels to buffer against potential delays, increasing warehousing costs and tying up capital. The optimal balance depends on factors like demand variability, supplier reliability, and the cost of holding inventory.
Delays in TAT and Their Impact on Supply Chain Efficiency
Delays in TAT at any stage of the supply chain create ripple effects, negatively impacting efficiency. For example, a delay in raw material delivery can halt production, leading to missed deadlines and lost sales. Similarly, delays in transportation can disrupt the timely delivery of finished goods to customers, impacting customer satisfaction and potentially damaging brand reputation. These delays often result in increased costs associated with expedited shipping, overtime pay, and potential penalties for late delivery. Consider a scenario where a manufacturer relies on a specific component from an overseas supplier. A delay in shipment due to unforeseen circumstances (e.g., port congestion, natural disaster) could cause a production standstill, resulting in significant financial losses and potentially impacting the entire supply chain.
Strategies for Improving TAT Across the Supply Chain
Improving TAT requires a holistic approach involving collaboration across all supply chain partners. Strategies include optimizing procurement processes to ensure timely sourcing of raw materials, implementing efficient inventory management systems to reduce lead times, and leveraging advanced technologies like RFID and real-time tracking for improved visibility. Streamlining logistics operations through route optimization and efficient warehousing practices is also crucial. Investing in robust supply chain planning software can aid in forecasting demand, optimizing inventory levels, and proactively identifying potential bottlenecks. Furthermore, fostering strong relationships with suppliers and logistics providers is essential for effective communication and collaborative problem-solving.
Process Diagram for Measuring and Improving TAT in a Supply Chain
Imagine a process flow diagram. The diagram begins with “Order Placement” and flows through “Order Processing,” “Procurement,” “Production,” “Quality Control,” “Warehousing,” “Shipping,” and finally “Delivery.” Each stage has a designated time measurement. These times are aggregated to calculate the overall TAT. The diagram also incorporates feedback loops at each stage. For example, data from “Quality Control” can be used to improve “Production” processes, reducing TAT. Similarly, data from “Delivery” informs improvements in “Shipping” and “Warehousing.” Regular monitoring of these times and the use of Key Performance Indicators (KPIs) such as on-time delivery rate and order fulfillment cycle time enable identification of bottlenecks and areas for improvement. By analyzing the data, specific actions can be taken to optimize each stage, leading to a reduction in overall TAT. For instance, if “Procurement” consistently shows delays, strategies like supplier diversification or negotiating shorter lead times can be implemented.
TAT and its Legal Implications
Turnaround time (TAT) isn’t just a metric for internal efficiency; it holds significant legal weight, particularly when incorporated into contracts. Failure to meet agreed-upon TATs can lead to legal repercussions, impacting business relationships and potentially resulting in financial penalties. Understanding the legal implications of TAT is crucial for mitigating risk and ensuring compliance.
Failing to meet contractually obligated TATs can expose businesses to various legal challenges. The specific consequences depend on the nature of the contract, the severity of the breach, and the applicable jurisdiction’s laws. For instance, consistent failure to meet deadlines in a service contract could constitute a breach of contract, allowing the client to seek remedies such as damages for losses incurred due to the delay, specific performance requiring the service provider to fulfill the contract within a reasonable timeframe, or even contract termination. In some cases, particularly in contracts involving critical services or time-sensitive deliverables, significant delays could result in lawsuits and substantial financial penalties.
Contractual Incorporation of TAT
Service Level Agreements (SLAs) frequently incorporate TAT as a key performance indicator (KPI). These agreements define the expected level of service and specify the consequences of not meeting those standards. A well-drafted SLA clearly Artikels the TAT for specific services, defining what constitutes a breach, and specifying the remedies available to the client in case of non-compliance. For example, an SLA for a web hosting provider might stipulate a TAT of four hours for resolving server downtime incidents. Failure to meet this TAT could result in a service credit or a reduction in the monthly fee. The inclusion of specific, measurable, achievable, relevant, and time-bound (SMART) TATs within SLAs is crucial for both parties to understand their obligations and the consequences of non-compliance.
Documentation and Tracking of TAT for Compliance
Effective documentation and tracking of TAT are essential for demonstrating compliance and mitigating legal risk. Businesses should maintain meticulous records of all TAT-related activities, including initial agreements, progress updates, and any instances of delays. This documentation should be easily accessible and readily available in case of disputes. Methods for tracking TAT may involve using project management software, specialized time-tracking tools, or even simple spreadsheets. Regular monitoring of TAT against agreed-upon targets allows for proactive identification and mitigation of potential issues. This approach allows for timely intervention to prevent breaches and avoids the need for costly legal interventions later. Moreover, robust documentation serves as evidence in case of legal disputes, supporting claims of compliance or demonstrating efforts to rectify delays. Examples of effective documentation include signed contracts with clearly stated TATs, detailed project timelines, and logs of communication regarding delays and their resolution.
TAT in Different Business Sectors
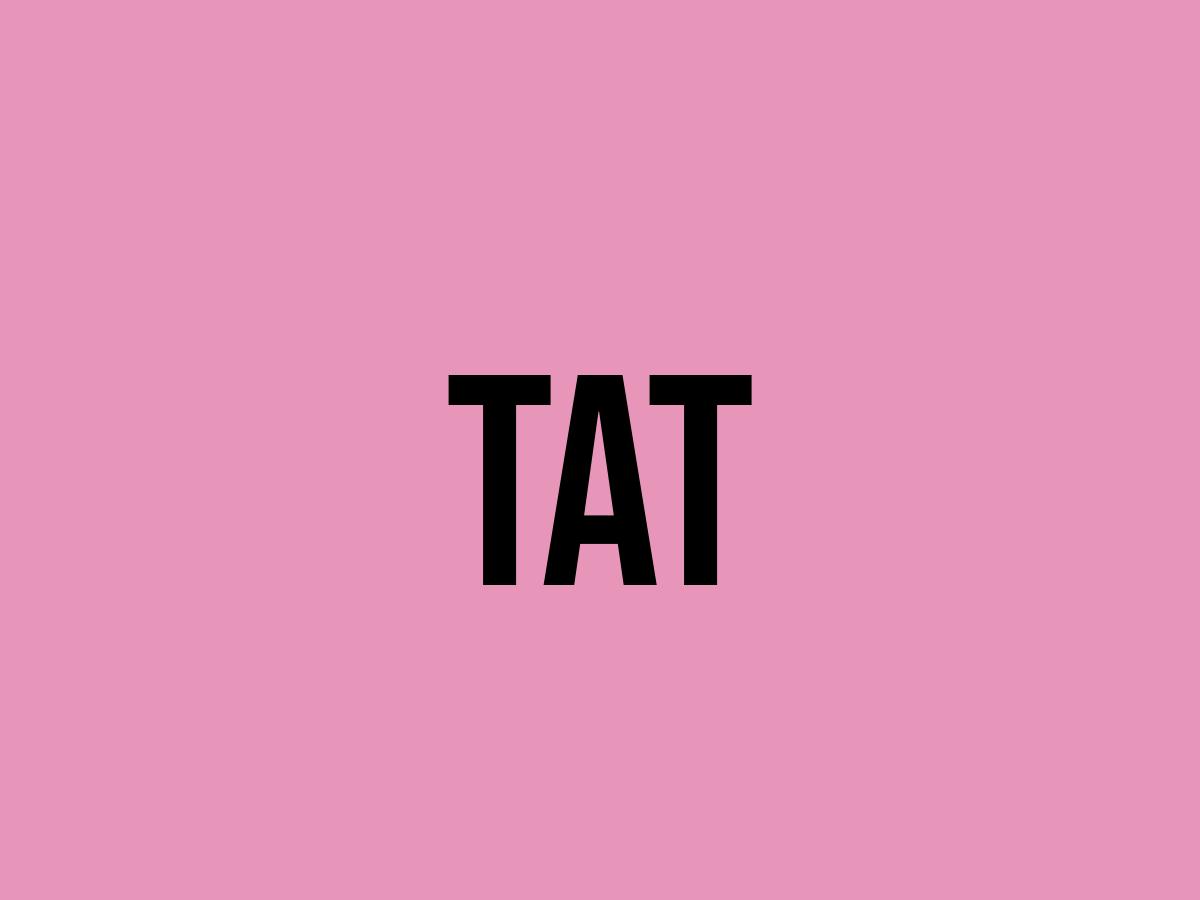
Turnaround time (TAT) significantly impacts customer satisfaction and overall business efficiency. However, the acceptable and achievable TAT varies dramatically across different sectors, influenced by factors such as the complexity of the service or product, regulatory requirements, and industry standards. Understanding these sector-specific differences is crucial for effective TAT management.
TAT in the Finance Sector
The finance sector, encompassing banking, investment, and insurance, often operates under stringent regulatory frameworks and faces high expectations for rapid processing. TATs for tasks like loan approvals, transaction processing, and insurance claims settlements are critical to customer experience and operational efficiency. Challenges include complying with regulatory requirements, managing large transaction volumes, and ensuring data security. Banks, for example, are increasingly leveraging automation and AI to streamline processes and reduce TAT for loan applications, while insurance companies utilize advanced analytics to expedite claims processing and reduce fraud.
TAT in the Healthcare Sector
Healthcare providers face unique challenges in managing TAT, particularly concerning diagnostic testing, treatment procedures, and appointment scheduling. Longer TATs can lead to delayed diagnoses, compromised patient care, and increased healthcare costs. Regulatory compliance, resource allocation, and the complexity of patient cases contribute to these challenges. Hospitals and clinics are adopting electronic health records (EHRs) and telehealth technologies to improve communication, streamline workflows, and reduce wait times for appointments and test results. Efficient scheduling systems and optimized staffing levels also play a significant role in reducing TAT.
TAT in the Technology Sector
The technology sector, characterized by rapid innovation and intense competition, prioritizes quick turnaround times for software development, bug fixes, and customer support. Meeting aggressive deadlines and responding swiftly to customer issues are crucial for maintaining a competitive edge. Challenges include managing complex projects, integrating diverse technologies, and ensuring software quality. Agile methodologies, DevOps practices, and automated testing are common strategies employed by technology companies to shorten development cycles and improve the speed of issue resolution. Companies like Google and Amazon prioritize continuous integration and continuous delivery (CI/CD) to ensure rapid software releases and updates.
Visual Representation of TAT

Understanding Turnaround Time (TAT) is crucial for effective business operations. Visual representations are invaluable tools for quickly grasping the impact of TAT on various processes and for effectively communicating this data to stakeholders. Clear visualizations aid in identifying bottlenecks, improving efficiency, and making data-driven decisions.
Visualizing the impact of short versus long TAT on a business process can be effectively done through a simple illustration.
Illustrative Comparison of Short and Long TAT
Imagine two parallel pathways representing the processing of a customer order. The first pathway, representing a short TAT, is depicted as a smooth, swift flowing river, with a clearly marked starting point (order received) and endpoint (order delivered). The river flows rapidly, with minimal obstacles, symbolized by small, easily navigable rocks. The time taken for the water to flow from start to finish is short, visually represented by a shorter distance between the start and end points. This pathway is labeled “Short TAT: Efficient Process.” The second pathway, illustrating a long TAT, is depicted as a sluggish, meandering stream, full of large, impassable boulders representing delays and bottlenecks. The stream winds considerably, increasing the distance between the starting and ending points. The time taken for the water to navigate this path is significantly longer. This pathway is labeled “Long TAT: Inefficient Process.” This visual immediately communicates the efficiency gains achieved by reducing TAT.
Communicating TAT Data with Charts
A Gantt chart is an effective way to visually communicate TAT data to stakeholders, particularly in project management.
Gantt Chart for TAT Visualization
A Gantt chart would display tasks on the horizontal axis, representing the different stages of a business process. The vertical axis would represent time, typically in days or weeks. Each task would be represented by a horizontal bar, with the length of the bar corresponding to the duration of the task. The start and end points of each bar clearly indicate the TAT for that specific task. Different colors could be used to represent different teams or departments responsible for each task. Critical path analysis can be integrated to highlight the most time-consuming tasks impacting the overall TAT. This visual clearly shows the duration of each process step and potential bottlenecks, allowing for easier identification of areas for improvement. For example, a Gantt chart could show the TAT for order processing, from order placement to shipment, highlighting delays at specific stages like order verification or inventory management. By overlaying planned TAT with actual TAT, the chart can also clearly show variances and areas needing attention.