What license do I need to start a welding business? This crucial question hinges on a complex interplay of local, state, and federal regulations. Launching a welding business requires navigating a maze of permits, licenses, and insurance requirements, ensuring compliance with safety standards, and understanding tax obligations. This guide unravels the complexities, providing a clear path to successfully establishing your welding enterprise.
From securing the necessary business licenses and permits to understanding zoning regulations and insurance needs, we’ll cover every step. We’ll also delve into crucial safety regulations, professional certifications, and tax requirements. By the end, you’ll have a comprehensive understanding of the legal and regulatory landscape for starting a welding business.
Business Licenses and Permits
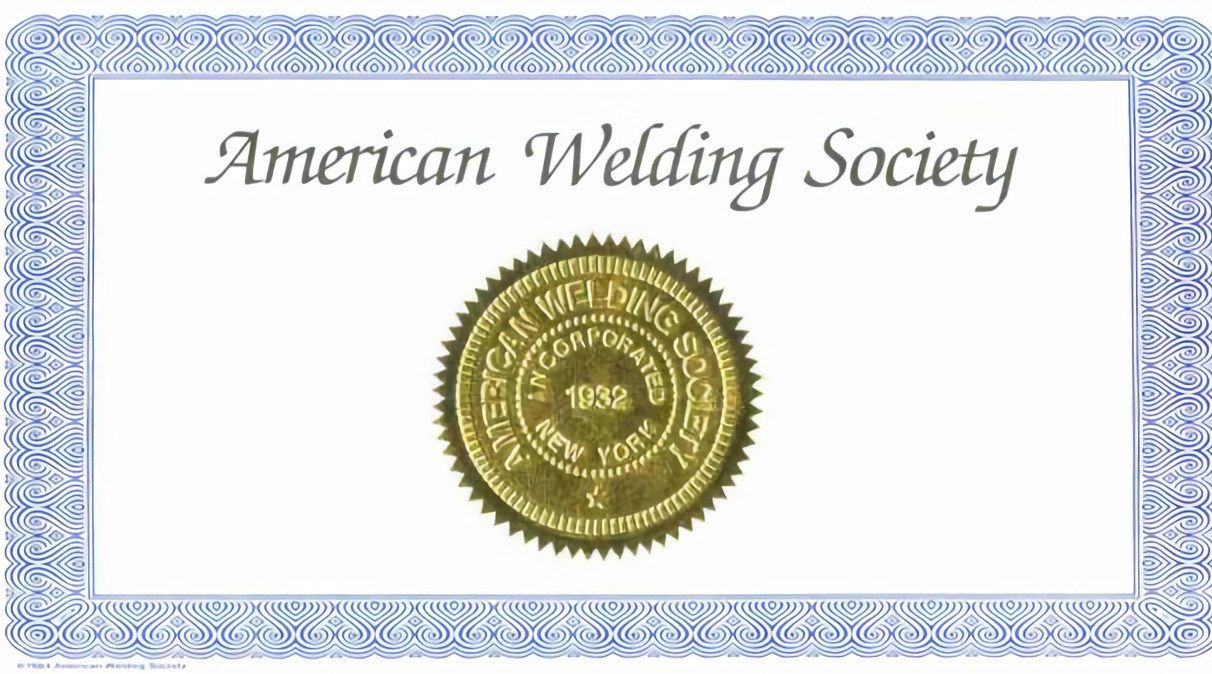
Starting a welding business requires navigating the complex landscape of local, state, and federal regulations. Securing the necessary licenses and permits is crucial for legal operation and avoiding potential penalties. This process can vary significantly depending on your location and the specific services offered. Understanding these requirements is a critical first step in establishing a successful and compliant welding business.
Obtaining Business Licenses and Permits: A General Overview
The process of obtaining business licenses and permits typically involves three levels of government: local, state, and federal. At the local level, you’ll likely need a general business license from your city or county. State requirements often include contractor’s licenses, especially if you’re working on construction projects. Federal regulations may apply depending on your business activities, potentially involving permits related to hazardous materials handling or environmental protection. Each level has its own application process, fees, and required documentation.
Common Licenses and Permits for Welding Businesses
The specific licenses and permits required for a welding business will vary depending on location and the nature of the work performed. However, the following table provides a general overview of common requirements categorized by jurisdiction.
Jurisdiction | License/Permit Type | Description | Acquisition Process |
---|---|---|---|
Local | General Business License | Authorizes operation of a business within the city or county. | Apply online or in person at the local government office. Typically requires business name registration, tax identification number, and business address. Fees vary. |
State | Contractor’s License | Required for businesses performing construction-related welding services. May involve specific requirements based on the type of welding and project scope. | Application to the state contractor’s licensing board. Often involves examinations, background checks, insurance requirements, and fees. |
State | Sales Tax Permit | Required to collect and remit sales tax on services provided. | Application through the state’s revenue department. Usually involves registering the business and obtaining a tax ID number. |
Federal | Employer Identification Number (EIN) | Required if you hire employees or operate as a corporation or partnership. | Apply online through the IRS website. This is a free process. |
Local/State (Potentially) | Hazardous Waste Permits | May be required if the welding process generates hazardous waste materials. | Application to the relevant environmental agency. Requirements vary significantly based on the type and quantity of waste generated. This often includes detailed waste management plans and environmental impact assessments. Fees can be substantial. |
Examples of Specific License and Permit Applications
A general business license application typically requires providing information about the business owner(s), the business address, the nature of the business, and the intended business activities. Supporting documentation might include proof of business registration, tax identification numbers (EIN or SSN), and potentially a business plan. Fees vary by location.
Contractor’s license applications are often more rigorous, demanding proof of experience, completion of relevant training or education, passing a licensing exam, proof of insurance (general liability and workers’ compensation), and potentially background checks. These applications often require detailed information about the business’s operations and financial stability. Fees are usually higher and vary by state.
Acquiring a hazardous waste permit involves a complex application process. This will necessitate a comprehensive description of the welding processes used, the types and quantities of hazardous waste generated, the proposed waste management plan, and potentially an environmental impact assessment. Fees vary greatly based on the complexity of the operation and the environmental risk assessment. The application will likely require detailed documentation, including safety data sheets (SDS) for all materials used and waste generated.
Zoning and Land Use Regulations: What License Do I Need To Start A Welding Business
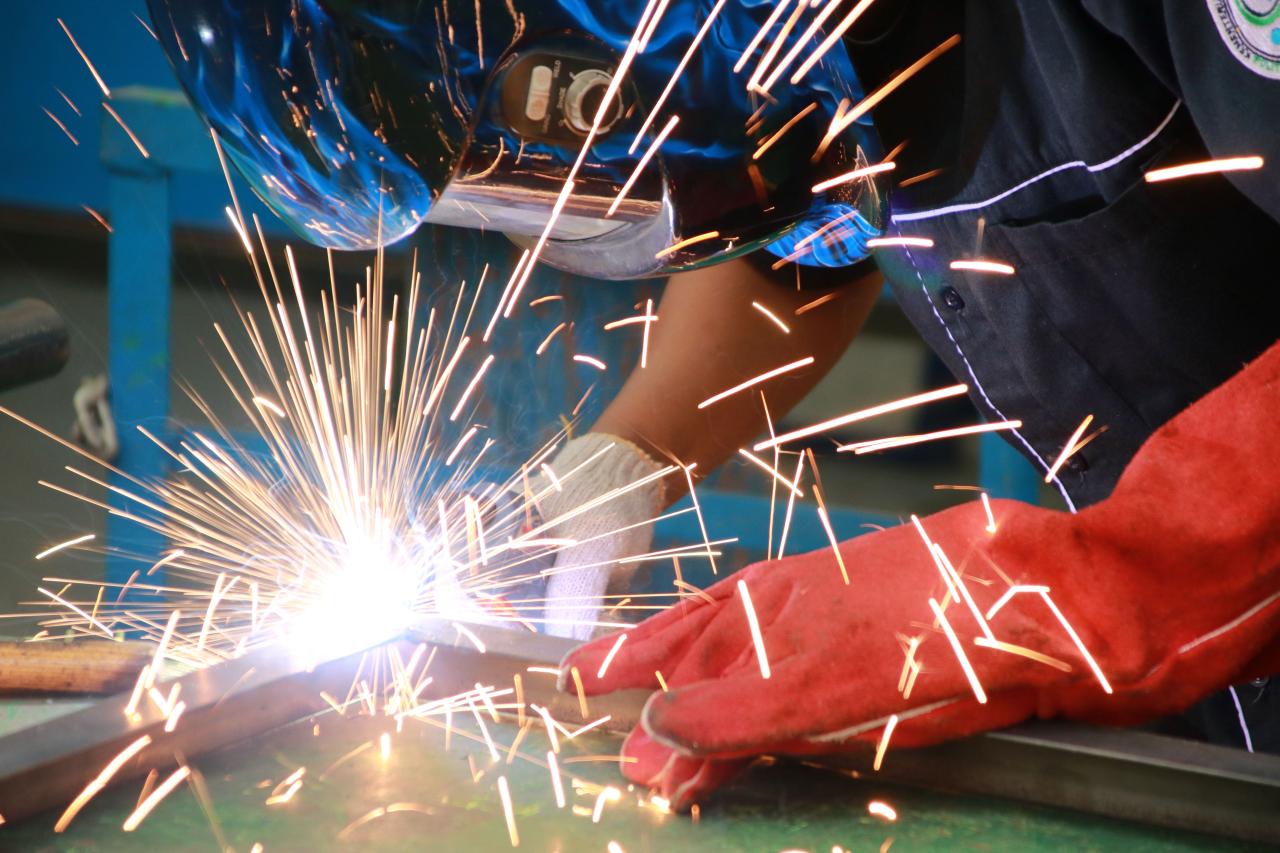
Operating a welding business requires careful consideration of local zoning and land use regulations. These regulations vary significantly depending on location and the type of welding operation. Understanding these rules is crucial to avoid legal issues and ensure your business operates smoothly. Failure to comply can result in fines, cease-and-desist orders, and even business closure.
Zoning Regulations for Different Business Locations
The zoning regulations governing your welding business will differ drastically depending on whether you operate from your home, a rented space, or a commercial property. Residential zones typically have strict limitations on industrial activities, including welding, due to concerns about noise, fire hazards, and air quality. Rented spaces might fall under commercial or industrial zoning, offering more flexibility but still subject to specific regulations. Commercial properties zoned for industrial use generally provide the most leeway for welding operations, though specific restrictions may still apply. For example, a business operating in a residential area might be restricted from welding after certain hours, while a business in an industrial park might face limitations on the types of welding processes permitted due to environmental concerns.
Restrictions on Welding Activities Based on Zoning Classifications, What license do i need to start a welding business
Zoning classifications directly impact the types of welding activities permitted. For instance, a residential zone might completely prohibit welding, or allow only limited activities such as minor repairs with specific, low-emission equipment. Commercial zones may allow more extensive welding operations, but could restrict activities like plasma cutting due to noise or air pollution concerns. Industrial zones generally offer the most flexibility but might still impose limitations based on factors like proximity to residential areas, environmental regulations, and the specific type of welding involved (e.g., arc welding versus laser welding). These restrictions are often detailed in the local zoning ordinances, which should be consulted thoroughly. Failure to adhere to these stipulations can lead to penalties. For example, a business exceeding permitted noise levels in a commercial zone could receive a noise violation.
Obtaining Zoning Variances or Permits for Welding Operations
If your welding business plans exceed the allowances of your current zoning, you may need to apply for a zoning variance or special permit. This process typically involves submitting a detailed application to the local zoning authority, outlining your proposed welding operations and demonstrating how they will comply with all relevant regulations and minimize any potential negative impacts on the surrounding community. The application often requires detailed plans, environmental impact assessments, and sometimes, public hearings. The zoning authority will review the application and determine whether the variance or permit should be granted. The approval process can vary depending on the jurisdiction and the complexity of the application. For example, a variance request to operate a large-scale welding fabrication shop in a mixed-use zone might require more extensive documentation and a longer review period compared to a request for a small, low-impact welding repair business in a commercial zone.
Checklist for Compliance with Local Zoning Ordinances
Before starting your welding business, it’s crucial to ensure complete compliance with local zoning ordinances. This checklist Artikels key steps:
- Identify your business location’s zoning classification.
- Review the local zoning ordinances for regulations specific to welding businesses.
- Determine if your planned welding activities comply with the zoning regulations.
- If not, determine if a zoning variance or special permit is required.
- Prepare and submit a complete application for any necessary variances or permits.
- Obtain all necessary approvals from the zoning authority.
- Maintain accurate records of all zoning compliance documentation.
Insurance Requirements
Securing the right insurance is paramount for any welding business, protecting your assets and mitigating potential financial risks associated with accidents, injuries, and property damage. Failure to obtain adequate coverage can lead to significant financial losses and legal liabilities. This section Artikels the essential insurance types, coverage amounts, and provider considerations for welding businesses.
General Liability Insurance
General liability insurance protects your business from financial losses due to third-party bodily injury or property damage caused by your operations. This includes incidents occurring on your premises, at a client’s site, or even during transportation of equipment. For a welding business, this coverage is crucial as sparks, hot metal, and equipment malfunctions can easily lead to accidents. Recommended coverage amounts typically range from $1 million to $2 million per occurrence, with an aggregate limit of $2 million to $5 million. This ensures sufficient protection against significant claims. Higher coverage limits might be advisable depending on the scale and complexity of your operations.
Workers’ Compensation Insurance
Workers’ compensation insurance is legally mandated in most jurisdictions for businesses with employees. It covers medical expenses and lost wages for employees injured on the job, regardless of fault. Welding is inherently risky, with potential for burns, eye injuries, and respiratory problems. Therefore, comprehensive workers’ compensation insurance is vital. The required coverage amount varies by state and is typically determined by your payroll. It’s crucial to accurately assess your payroll to ensure sufficient coverage. Failure to maintain adequate workers’ compensation insurance can result in severe penalties and legal repercussions.
Commercial Auto Insurance
If your welding business involves transporting equipment or employees to job sites, commercial auto insurance is essential. This protects your business from liability arising from accidents involving your company vehicles. The policy should cover bodily injury and property damage liability, as well as collision and comprehensive coverage for vehicle damage. Coverage amounts should be sufficient to cover potential damages and legal fees resulting from accidents. Consider the size and type of vehicles used to determine the appropriate coverage levels. Uninsured/underinsured motorist coverage is also recommended to protect against accidents involving drivers without sufficient insurance.
Insurance Provider Comparison
Different insurance providers offer varying coverage options and pricing for welding businesses. Factors such as your business size, location, and claims history influence premiums. Some providers specialize in insuring high-risk industries like welding, offering tailored policies and competitive rates. Others may offer broader coverage but at a higher cost. It’s advisable to obtain quotes from multiple providers to compare coverage options and pricing before making a decision. Consider factors beyond price, such as the provider’s reputation, claims handling process, and customer service.
Sample Insurance Policy Comparison Chart
Insurance Provider | General Liability ($1M/$2M) | Workers’ Compensation (Annual Premium Estimate) | Commercial Auto ($1M/$2M) | Other Key Features |
---|---|---|---|---|
Provider A | $1,200 | $3,000 (based on $50,000 payroll) | $800 | 24/7 claims support, online portal access |
Provider B | $1,500 | $2,800 (based on $50,000 payroll) | $950 | Discounts for safety training programs |
Provider C | $1,000 | $3,200 (based on $50,000 payroll) | $750 | Specialized coverage for welding businesses |
*Note: These are sample prices and may vary significantly based on individual circumstances. Obtain quotes from multiple providers for accurate pricing.*
Safety Regulations and Compliance
Operating a welding business necessitates strict adherence to safety regulations to protect both employees and the public. Failure to comply can result in significant fines, legal repercussions, and, most importantly, serious injuries or fatalities. Understanding and implementing appropriate safety measures is paramount for the success and ethical operation of any welding business.
Occupational Safety and Health Administration (OSHA) Regulations for Welding Businesses
The Occupational Safety and Health Administration (OSHA) sets forth comprehensive regulations concerning workplace safety, many of which are specifically relevant to welding operations. These regulations cover various aspects, from the proper use of personal protective equipment (PPE) to the safe handling and storage of welding materials. Key OSHA standards impacting welding businesses include those addressing hazard communication, respiratory protection, fire protection, and electrical safety. Understanding these standards and their implications is crucial for ensuring a safe working environment. Specific standards frequently cited include 29 CFR 1910.252 (Welding, Cutting, and Brazing) and related subparts. These standards detail requirements for ventilation, fire prevention, and the use of appropriate PPE. Regular review and updates on OSHA’s website are essential to maintain compliance with evolving safety standards.
Essential Safety Equipment and Procedures
Compliance with OSHA standards requires the implementation of specific safety procedures and the provision of essential safety equipment. This equipment is designed to mitigate the various hazards associated with welding. Essential items include, but are not limited to: appropriate welding helmets with appropriate shade lenses for the welding process being used; flame-resistant clothing, including jackets, gloves, and leggings; safety footwear with metatarsal guards; respirators designed to filter out welding fumes and particulate matter; fire extinguishers appropriately rated for welding fires (typically Class A, B, and C); and well-maintained welding equipment regularly inspected for leaks or malfunctions. Furthermore, procedures should be in place for the safe handling and storage of compressed gases, the proper ventilation of welding areas, and emergency response protocols. Regular training and competency assessments for employees on the proper use and maintenance of safety equipment are also mandatory.
Workplace Hazards and Risk Mitigation Strategies
Welding presents numerous potential workplace hazards. Effective risk mitigation requires a proactive approach that addresses these hazards directly.
- Arc Eye (flash burns): Mitigated by the consistent use of appropriately shaded welding helmets and ensuring all personnel in the vicinity wear appropriate eye protection.
- Burns (thermal and electrical): Mitigated through the use of flame-resistant clothing, proper grounding of equipment, and safe handling procedures for hot materials.
- Fumes and Gases: Mitigated by ensuring adequate ventilation, the use of appropriate respirators, and the selection of low-fume welding processes when feasible.
- Fire Hazards: Mitigated by the use of fire-resistant materials, proper storage of flammable materials, readily accessible fire extinguishers, and regular fire drills.
- Electrical Hazards: Mitigated by proper grounding of equipment, regular inspection of electrical cords and connections, and adherence to lockout/tagout procedures when working on electrical systems.
- Noise Hazards: Mitigated by using hearing protection, regular hearing tests, and minimizing noise levels through appropriate work practices.
Creating a Comprehensive Safety Plan
A comprehensive safety plan is essential for a welding business. This plan should Artikel procedures for all aspects of workplace safety, including emergency response. The plan should include:
- Hazard Identification and Risk Assessment: A detailed inventory of potential hazards and a corresponding assessment of the risks associated with each hazard.
- Safety Procedures and Training: Detailed procedures for safe welding practices, emergency procedures, and regular employee training programs.
- Personal Protective Equipment (PPE) Program: A program outlining the required PPE, its proper use, maintenance, and regular inspection.
- Emergency Response Plan: Clearly defined procedures for responding to various emergencies, including fire, electrical shock, and medical emergencies. This plan should include designated escape routes, assembly points, and contact information for emergency services.
- Record Keeping: Maintenance of accurate records of safety training, inspections, accidents, and incidents. These records are essential for demonstrating compliance with OSHA regulations.
Professional Certifications and Qualifications
Obtaining professional welding certifications is crucial for both individual welders and their businesses. These certifications demonstrate a high level of skill and competency, leading to increased earning potential and enhanced business credibility. They also often fulfill requirements for specific jobs and projects, opening doors to a wider range of opportunities.
Professional welding certifications offer several key benefits. For individual welders, certification validates their skills, making them more competitive in the job market and potentially commanding higher wages. For businesses, certified welders improve the quality of work, reduce liability risks, and enhance the company’s reputation, attracting more clients and securing more lucrative contracts. This ultimately translates to increased profitability and a stronger market position.
Relevant Welding Certifications and Requirements
Several organizations offer widely recognized welding certifications. The specific requirements vary depending on the certification level and the certifying body. These requirements typically include a combination of documented experience, theoretical knowledge, and practical skills demonstrated through rigorous testing.
- American Welding Society (AWS) Certifications: The AWS offers a range of certifications, from basic certifications covering specific welding processes (like SMAW, GMAW, GTAW) to more advanced certifications specializing in specific materials or applications. Requirements often include documented hours of welding experience and successful completion of both written and practical examinations. The AWS certifications are highly respected within the industry.
- American Society of Mechanical Engineers (ASME) Certifications: ASME certifications are crucial for welders working on pressure vessels, boilers, and other critical components. These certifications typically require extensive experience and rigorous testing, focusing on the specific codes and standards relevant to pressure vessel fabrication.
- Other National and International Certifications: Numerous other organizations, both nationally and internationally, offer welding certifications. These certifications often cater to specific industries or regions, and their requirements will vary accordingly. Examples include certifications from the Canadian Welding Bureau (CWB) and various European standards organizations.
Examples of Enhanced Credibility and Client Attraction
A welding business with certified welders immediately projects professionalism and competence. Clients are more likely to trust a company that demonstrates a commitment to quality and safety through certifications. For example, a company bidding on a large-scale construction project requiring adherence to stringent ASME codes will have a significant advantage if its welders possess the relevant ASME certifications. Similarly, a business specializing in high-end automotive repair will benefit from welders certified in specialized welding techniques used in that sector. The presence of certifications can be a deciding factor for clients seeking reliable and qualified professionals, leading to increased business and higher project fees.
Obtaining a Welding Certification: Process and Requirements
The process of obtaining a welding certification generally involves several steps. First, the welder must meet the prerequisite requirements, which may include a certain amount of documented welding experience or completion of relevant educational courses. Next, the welder registers for the certification examination with the chosen certifying body. The examination typically includes a written test assessing theoretical knowledge and a practical test demonstrating welding skills. The practical test often involves producing welds to specific standards, which are then inspected and evaluated by certified examiners. Upon successful completion of both the written and practical examinations, the welder is awarded the certification. The specific requirements and procedures will vary depending on the chosen certification and the certifying body, so it is crucial to consult the relevant organization’s guidelines.
Tax Requirements and Registration

Starting a welding business involves navigating various tax obligations at the federal, state, and local levels. Understanding these requirements is crucial for maintaining compliance and avoiding potential penalties. This section Artikels the key tax responsibilities for welding businesses, including registration processes and crucial deadlines.
Sales Tax
Sales tax is a consumption tax levied on the sale of goods and services. As a welding business, you’ll likely collect sales tax on the services you provide and any materials you sell to clients. The specific sales tax rate varies by state and even by locality within a state. It’s essential to register with your state’s tax agency to obtain a sales tax permit and understand the applicable rates for your business location. Accurate record-keeping is vital, meticulously tracking sales, the tax collected, and timely filing of returns. Failure to comply can result in significant penalties and interest charges. For example, a welding business operating in California needs to register with the California Department of Tax and Fee Administration (CDTFA) and follow their guidelines for sales tax collection and remittance.
Income Tax
Welding businesses, like other businesses, are subject to income tax. The structure of your business (sole proprietorship, partnership, LLC, or corporation) will determine how your business income is reported. Sole proprietors and partners report business income and expenses on their personal income tax returns (Form 1040, Schedule C), while LLCs and corporations file separate tax returns. Accurate record-keeping of all income and deductible business expenses is critical for minimizing your tax liability. For example, the cost of welding equipment, materials, and employee wages are typically deductible expenses.
Employer Identification Number (EIN)
If you plan to hire employees, you’ll need to obtain an Employer Identification Number (EIN) from the IRS. An EIN is a unique tax identification number used by the IRS to identify your business for tax purposes. It’s used for various tax filings, including payroll taxes, and is separate from your personal Social Security number. Applying for an EIN is a straightforward process that can be completed online through the IRS website.
Federal, State, and Local Tax Compliance
Complying with tax regulations requires understanding the specific requirements at each level of government. Federal taxes include income tax, self-employment tax (if applicable), and employment taxes (if you have employees). State taxes may include sales tax, income tax, and potentially other business-related taxes. Local taxes can vary significantly and might include property taxes or business license fees. Regularly consulting the relevant tax agencies at the federal, state, and local levels is crucial for staying informed about changes in tax laws and deadlines.
Tax Calendar for a Welding Business
A well-organized tax calendar is essential for staying on top of tax deadlines. This is a sample calendar; specific dates may vary depending on your location and business structure.
Quarter | Tax Deadline | Tax Type |
---|---|---|
Q1 (Jan-Mar) | April 15th | Estimated income tax payments (if applicable), Quarterly payroll tax payments (if applicable) |
Q2 (Apr-Jun) | June 15th | Estimated income tax payments (if applicable), Quarterly payroll tax payments (if applicable) |
Q3 (Jul-Sep) | September 15th | Estimated income tax payments (if applicable), Quarterly payroll tax payments (if applicable) |
Q4 (Oct-Dec) | January 15th (following year) | Estimated income tax payments (if applicable), Quarterly payroll tax payments (if applicable), Annual income tax return |
Note: This is a simplified example, and actual deadlines may vary. Consult with a tax professional for personalized advice.