Why did the muffler quit the car business? This seemingly whimsical question opens a door to a surprisingly complex world of automotive engineering, economics, and environmental regulations. We’ll explore the life of a muffler—from its daily grind of silencing explosions to its eventual retirement—examining the mechanical failures, technological advancements, and market forces that contribute to its replacement. Prepare for a journey that blends mechanical realities with a touch of anthropomorphic storytelling.
This exploration delves into the common causes of muffler failure, such as rust and corrosion, comparing the longevity of various materials. We’ll trace the evolution of exhaust systems, highlighting key innovations and their impact on noise reduction and emissions. Further, we’ll examine economic factors influencing muffler demand, analyze the competitive landscape of the manufacturing industry, and discuss the role of environmental regulations in shaping muffler design. Finally, we’ll explore the vibrant aftermarket muffler industry, with its diverse offerings and performance characteristics.
The Literal Meaning
A muffler’s life is, quite literally, a noisy one. From the moment it’s welded into place, it’s subjected to a constant barrage of combustion engine sounds – a cacophony of explosions, vibrations, and the general rumble of internal combustion. Its primary function, of course, is to muffle these sounds, converting the raw, aggressive roar into a more socially acceptable hum. But this constant pressure, this relentless assault on its metallic composure, takes its toll.
The metaphorical “quitting” isn’t a sudden resignation; it’s a slow, corrosive process. Imagine years of enduring extreme temperatures, the constant vibration of the engine, and the corrosive effects of exhaust gases. Rust forms, tiny cracks appear, and the muffler’s ability to dampen sound gradually diminishes. The once-efficient silencer begins to let more and more noise escape, a slow, agonizing leak of its former capabilities. This is the muffler’s gradual disengagement from the car business – not a dramatic walkout, but a quiet, rusting fade-out.
A Muffler’s Final Day
The final day arrived with a particularly aggressive cough from the engine. The muffler, already weakened by years of service, felt a familiar tremor, but this time, it was different. A sharp crack resonated through its aging metal, a sound almost as loud as the exhaust it had been diligently silencing for so long. The crack grew, spreading like a spiderweb across its surface. A significant portion of its sound-dampening material fell away, showering the undercarriage with its decaying remains. The car’s engine roared, a raw, untamed sound that echoed the muffler’s own internal breakdown. The final vibration sent a shiver through its weakened structure, and with a final metallic groan, a significant part of the muffler separated, finally succumbing to years of relentless pressure and the inevitable corrosion of time. It was a quiet, unceremonious end, a fitting conclusion to a life spent in the often-unappreciated service of silencing the automotive world.
Mechanical Failures and Replacements
Muffler failure is a common automotive issue stemming from a combination of factors, ultimately leading to the need for replacement. Understanding the causes of failure and the lifespan variations among different muffler materials is crucial for both vehicle maintenance and cost prediction. This section details the common causes of muffler failure and compares the longevity and cost implications of different muffler materials.
The most prevalent reasons for muffler failure are rust, corrosion, and physical damage. Rust and corrosion, accelerated by exposure to road salt, moisture, and chemical pollutants, weaken the muffler’s structure, leading to holes, leaks, and eventual collapse. Physical damage, often resulting from impacts with road debris or off-road driving, can create dents, cracks, or punctures, compromising the muffler’s ability to effectively dampen exhaust noise and manage back pressure. The severity of damage dictates the extent of repair or the necessity of complete replacement.
Muffler Material Lifespan Comparison
The lifespan of a muffler is heavily influenced by the material used in its construction. Steel, aluminum, and stainless steel are common choices, each offering a different balance of durability, cost, and weight. Steel mufflers, while relatively inexpensive, are susceptible to rust and corrosion, leading to shorter lifespans, typically ranging from 3 to 5 years depending on environmental conditions. Aluminum mufflers offer improved corrosion resistance compared to steel, extending their lifespan somewhat, but they are more prone to dents and damage from impacts. Stainless steel mufflers, on the other hand, provide superior corrosion resistance and durability, resulting in significantly longer lifespans, often exceeding 10 years, making them a more cost-effective option in the long run, despite their higher initial cost.
Average Muffler Replacement Costs
The cost of muffler replacement varies considerably depending on the vehicle type, the material of the replacement muffler, and labor costs. Smaller vehicles generally require less expensive mufflers and less labor, resulting in lower overall costs. Larger vehicles, SUVs, and trucks often necessitate more substantial mufflers and more extensive labor, driving up the replacement cost. The choice of material also significantly impacts the cost, with stainless steel mufflers being the most expensive, followed by aluminum, and then steel. The following table provides estimated average costs for muffler replacement in various vehicle types.
Car Type | Average Cost | Material | Lifespan (Years) |
---|---|---|---|
Compact Car | $200 – $400 | Steel | 3-5 |
Sedan | $250 – $500 | Aluminized Steel | 5-7 |
SUV | $300 – $600 | Stainless Steel | 10+ |
Truck | $400 – $800 | Stainless Steel | 10+ |
The Evolution of Automotive Exhaust Systems
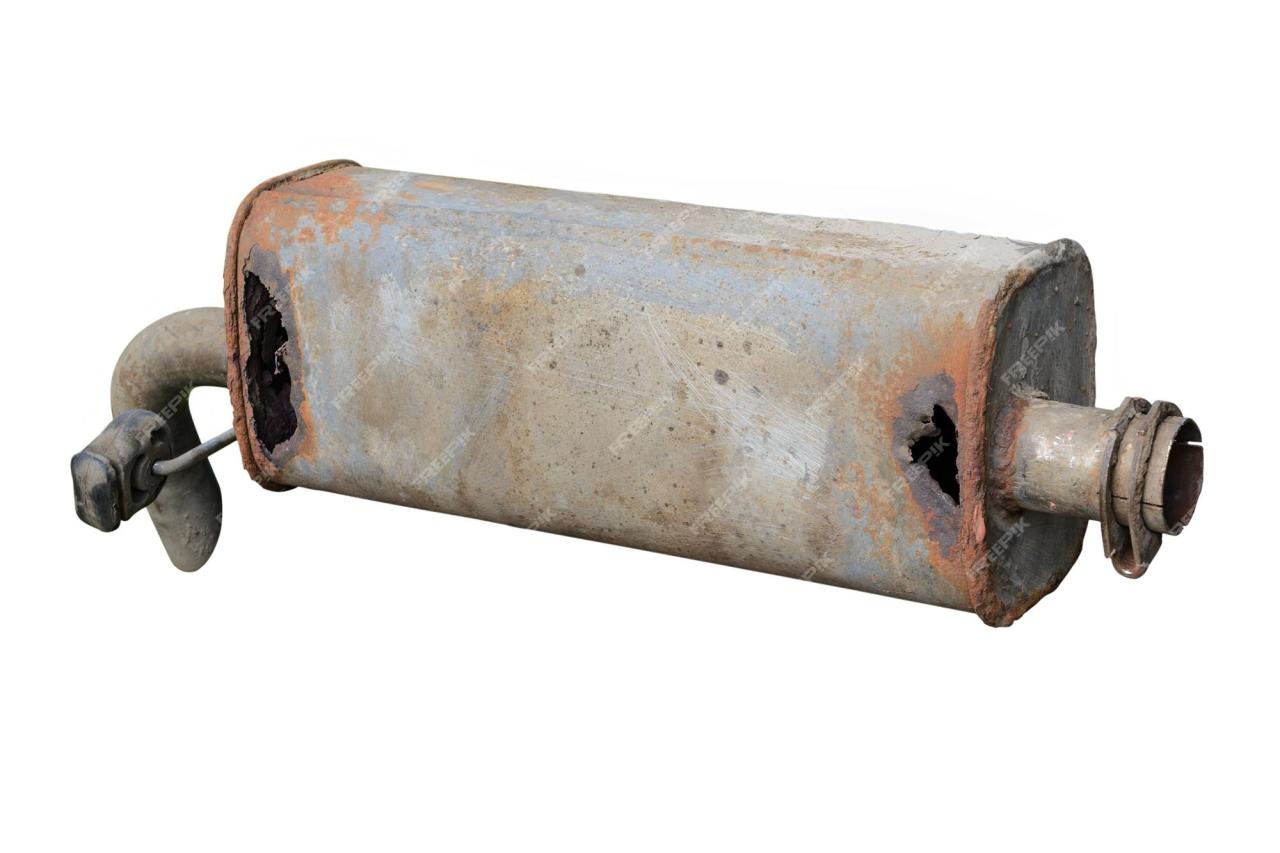
The automotive exhaust system has undergone a dramatic transformation since the dawn of the automobile, evolving from a simple pipe to a sophisticated assembly crucial for performance, noise reduction, and environmental compliance. Early designs focused primarily on directing exhaust gases away from the vehicle, while modern systems incorporate advanced technologies to minimize harmful emissions and improve fuel efficiency. This evolution is marked by significant innovations in muffler design and materials, reflecting both technological progress and increasingly stringent environmental regulations.
The earliest automobiles featured rudimentary exhaust systems—essentially a pipe extending from the engine to the rear of the vehicle. These lacked any significant silencing mechanisms, resulting in extremely loud and inefficient exhaust. As automobiles became more prevalent, the need for quieter and more efficient systems became apparent, leading to the development of the first rudimentary mufflers. These early mufflers were often simple chambers designed to partially absorb exhaust noise, offering minimal noise reduction compared to modern designs. The materials used were primarily cast iron or steel, reflecting the limitations of available manufacturing processes at the time.
Early Muffler Designs and Noise Reduction Techniques
Early muffler designs primarily focused on expanding the exhaust gases’ path to reduce their velocity and thus their noise. This was achieved through simple chambers and perforated tubes within the muffler casing. These designs, while offering some noise reduction, were relatively inefficient and often resulted in significant backpressure, negatively impacting engine performance. Materials science played a limited role in these early designs, with cast iron and steel being the predominant choices due to their durability and availability. The primary focus remained on achieving a balance between noise reduction and engine performance, a challenge that would continue to drive innovation in subsequent decades. A common design incorporated baffles within a chamber to further dampen sound waves. These baffles were often simple plates or perforated tubes, and their arrangement significantly influenced the muffler’s effectiveness.
The Rise of Resonator Technology and Advanced Materials
The development of resonator technology marked a significant advancement in muffler design. Resonators utilize the principles of acoustic resonance to cancel out specific frequencies of exhaust noise. By strategically placing resonators within the exhaust system, engineers could effectively reduce noise levels across a wider range of engine speeds. This technology, coupled with the introduction of more sophisticated internal geometries within mufflers, led to significant improvements in noise reduction. Simultaneously, advancements in materials science led to the adoption of lighter and more corrosion-resistant materials such as stainless steel and aluminized steel. These materials not only improved the durability and lifespan of mufflers but also contributed to overall vehicle weight reduction.
Modern Exhaust Systems and Emission Control
Modern exhaust systems are significantly more complex than their predecessors, incorporating a range of technologies designed to reduce both noise and harmful emissions. Catalytic converters, introduced in the 1970s, became integral components, chemically converting harmful pollutants such as carbon monoxide, nitrogen oxides, and unburned hydrocarbons into less harmful substances. This was a crucial step in meeting increasingly stringent emission standards. Further advancements include the integration of oxygen sensors and sophisticated engine control units (ECUs) to optimize the combustion process and minimize emissions. Modern mufflers often incorporate multiple chambers, resonators, and carefully designed internal geometries to achieve optimal noise reduction and minimal backpressure. The use of advanced materials, including high-temperature alloys and ceramic substrates in catalytic converters, ensures durability and effectiveness under demanding operating conditions. The integration of particulate filters (DPFs) in diesel engines represents another significant advancement, trapping soot particles and further reducing harmful emissions.
Economic and Market Factors: Why Did The Muffler Quit The Car Business
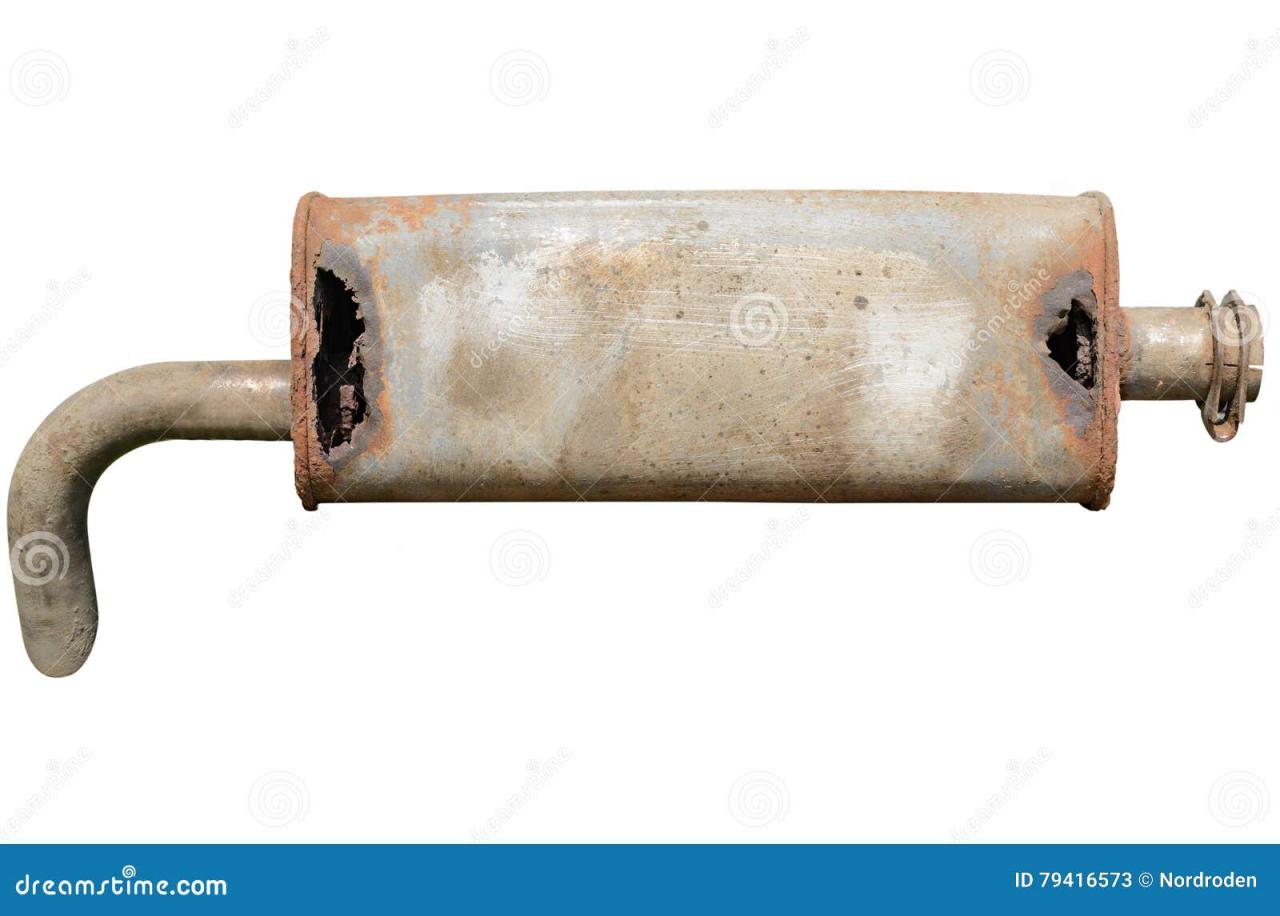
The automotive muffler market, like any other segment of the automotive parts industry, is significantly influenced by broader economic conditions and market trends. Fluctuations in fuel prices, economic recessions, and consumer spending habits all play a crucial role in determining the demand for replacement and aftermarket mufflers. Furthermore, the competitive landscape, marked by both large multinational corporations and smaller specialized manufacturers, shapes pricing strategies and product innovation.
Economic factors such as recessionary periods directly impact consumer spending on discretionary items, including automotive repairs and upgrades. During economic downturns, individuals are more likely to postpone non-essential vehicle maintenance, leading to a decrease in demand for replacement mufflers. Conversely, periods of economic growth generally see an increase in consumer spending, boosting demand. Fuel prices also exert a significant influence; high fuel costs encourage consumers to seek better fuel efficiency, sometimes leading to modifications that affect the exhaust system, including muffler replacements. Conversely, low fuel prices might reduce the urgency of such modifications.
Major Players in the Automotive Muffler Manufacturing Industry
Several key players dominate the global automotive muffler manufacturing industry. These companies range from large multinational corporations with diverse product portfolios to smaller, specialized manufacturers focusing on specific market segments or technological niches. While precise market share data fluctuates and is often proprietary, some of the most prominent players include companies like Magna International, Tenneco (now part of Aptiv), and Walker Exhaust. These companies often supply original equipment manufacturers (OEMs) as well as the aftermarket. Other significant players exist regionally, catering to specific geographical markets or specializing in certain muffler technologies. The competitive landscape is dynamic, with mergers, acquisitions, and technological advancements continuously reshaping the industry.
Comparison of Muffler Brands
The following table compares several prominent muffler brands, highlighting their price ranges, typical materials used, and key features. Note that prices are approximate and can vary based on retailer, specific model, and vehicle application. The features listed represent common offerings, and specific models may include additional or different options.
Brand | Price Range (USD) | Material | Key Features |
---|---|---|---|
Walker | $50 – $200 | Aluminized steel, stainless steel | Wide range of applications, good durability, often offered at competitive prices. |
Magnaflow | $100 – $500+ | Stainless steel, aluminized steel | Known for performance-oriented designs, often featuring increased flow and a more aggressive sound. Higher price reflects premium materials and design. |
Flowmaster | $100 – $400+ | Stainless steel, aluminized steel | Widely recognized for its distinct sound profiles, catering to different preferences from mild to aggressive. Offers a range of performance and sound options. |
Borla | $200 – $800+ | Stainless steel | Premium brand known for high-quality stainless steel construction and performance-focused designs. Often features a more refined sound than some competitors. High price reflects premium materials and craftsmanship. |
Environmental Regulations and Emissions
Mufflers, while primarily known for noise reduction, play a crucial, albeit indirect, role in controlling vehicle emissions. Their design and function are intrinsically linked to the overall exhaust system, which has evolved significantly in response to increasingly stringent environmental regulations.
The primary function of a muffler is to dampen the noise produced by the combustion engine. However, the exhaust gases passing through the muffler also contribute to overall emissions. The design of the muffler, including its internal baffles and chambers, influences the flow and pressure of these gases, indirectly impacting the efficiency of downstream emission control devices. A poorly designed or damaged muffler can negatively affect the performance of these devices, leading to increased emissions.
The Impact of Stricter Environmental Regulations on Muffler Design
The implementation of stricter emission standards, such as those related to hydrocarbons (HC), carbon monoxide (CO), and nitrogen oxides (NOx), has driven significant changes in muffler design and manufacturing. Early mufflers were relatively simple, prioritizing noise reduction over precise gas flow management. Modern mufflers, however, often incorporate features designed to optimize the flow of exhaust gases to maximize the effectiveness of catalytic converters and other emission control technologies. For example, the internal structure of a muffler might be optimized to ensure a uniform gas flow across the catalytic converter, preventing localized hotspots that can reduce its efficiency. Furthermore, the materials used in muffler construction have also evolved to withstand higher temperatures and pressures associated with modern, higher-performance engines while maintaining durability and preventing premature failure that could compromise emission control. Manufacturers now frequently utilize advanced materials and construction techniques to meet these demanding requirements. The shift towards lighter-weight materials also contributes to improved fuel economy, indirectly supporting emission reduction goals.
Interaction Between Mufflers and Emission Control Devices
Catalytic converters are the most prominent emission control device interacting directly with the muffler. Located downstream of the muffler, the catalytic converter relies on a consistent and even flow of exhaust gases to effectively convert harmful pollutants into less harmful substances. A restricted or damaged muffler can disrupt this flow, leading to reduced catalytic converter efficiency and increased emissions. Other emission control devices, such as particulate filters (DPF) in diesel engines, also benefit from a properly functioning muffler. The muffler’s design helps to ensure that the exhaust gases reach these filters at the correct temperature and pressure for optimal performance. A poorly functioning muffler can compromise the effectiveness of the entire emission control system, potentially leading to significant environmental consequences. Therefore, the design and maintenance of mufflers are integral to the overall efficiency and effectiveness of modern vehicle emission control systems.
The Aftermarket Muffler Industry

The aftermarket muffler industry caters to a diverse clientele, ranging from performance enthusiasts seeking enhanced power and sound to drivers prioritizing quieter operation or unique aesthetics. This sector offers a wide array of choices beyond the original equipment manufacturer (OEM) options, allowing for significant customization and personalization of a vehicle’s exhaust system. The market is driven by factors including individual preferences, vehicle modifications, and the desire to improve performance or alter the vehicle’s sound profile.
Types of Aftermarket Mufflers, Why did the muffler quit the car business
Aftermarket mufflers are broadly categorized based on their design and intended purpose. Performance mufflers prioritize increased engine power and a sportier exhaust note, often achieved through reduced back pressure. Conversely, quieter mufflers aim to minimize noise pollution, typically employing designs that dampen exhaust gases more effectively. Custom mufflers, fabricated to precise specifications, offer unparalleled flexibility in design and performance characteristics, allowing for tailored solutions to meet individual needs. Finally, universal fit mufflers offer a more affordable and readily available option, although they might require some modifications for optimal fitment.
Performance Characteristics of Aftermarket Mufflers
The performance characteristics of aftermarket mufflers vary considerably depending on their design and materials. Performance mufflers, for example, often feature larger diameter pipes and less restrictive internal components to minimize back pressure and maximize exhaust gas flow. This can lead to small gains in horsepower and torque, though the magnitude of these gains depends heavily on the vehicle and engine. Conversely, quieter mufflers prioritize noise reduction, sometimes at the expense of minor performance gains. Materials also play a role; stainless steel is popular for its durability and corrosion resistance, while other materials like aluminized steel offer a more budget-friendly option. The choice between these options often involves a trade-off between performance, longevity, and cost.
Sound Output Comparison: Stock vs. Aftermarket Mufflers
Imagine a comparative graph depicting sound output. The horizontal axis represents frequency (Hz), ranging from low to high pitches. The vertical axis represents sound pressure level (dB), indicating loudness. A line representing the stock muffler shows a relatively low and even sound pressure level across a limited frequency range, peaking in the mid-range frequencies and exhibiting a relatively muted and subdued tone. In contrast, a line representing a performance aftermarket muffler demonstrates a significantly higher sound pressure level across a broader frequency range, particularly in the lower frequencies, resulting in a deeper, more resonant, and louder exhaust note. The peak dB level would be notably higher for the aftermarket muffler. A quieter aftermarket muffler’s line would fall somewhere between the stock and performance muffler lines, with a lower overall dB level and less pronounced peaks in the frequency response, suggesting a quieter and less aggressive sound. The tonal qualities would be significantly different, with the stock muffler exhibiting a more muted and refined sound, while the performance muffler would have a deeper, more aggressive tone. The quieter aftermarket muffler would maintain a relatively subdued tone, though potentially with some enhancement in specific frequency ranges depending on the design.